|
|
現在位置:首頁
>> 產品與服務
>> NIIGATA重油發電機 |
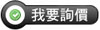 |
NIIGATA重油發電機 |
|
 |
22HLX Series
NIIGATA, Japan's
leading diesel engine
manufacturer, develops another
product resulting from
continuous innovation: the
22HLX medium speed
stationary diesel engine
series. |
|
The 22HLX
guarantees high performance with
a speed of 1 000 rpm or 900 rpm.
Avaliable in five models: 6L,
8L, 12V,16V and 18V, the 22HLX
is engineered to effectively
burn heavy fuel up to 700 cSt at
50 degC |
|
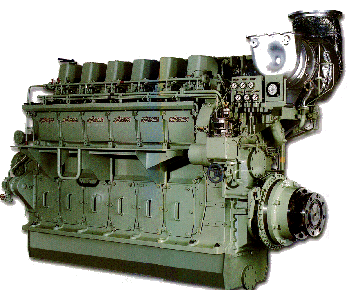 |
Superior
reliability and efficiency have
been achieved in the 22HLX
through careful research and
design implementation. Among the
outstanding features are the
engine's monoblock hanger type
crank case, induction hardened
crank shaft with large diameter
main and crank pin journals,
horizontal-split connecting
rods, segmented type (per
cylinder) cam shaft, cooling
system, as well as the intake
air duct, main cooling water
pipe and main lube oil pipe that
have been integrated in the
crank case. |
|
Compared to the
conventional diesel engine, the
brake mean effective pressure of
the 22HLX has been increased to
18%, and the mean piston speed
raised 8%. Its output rate of
24.4 MPa.m/s is noted as the
highest level in the world for
this engine size. |
|
Wider crank
case doors, 4-stud cylinder
heads, and the push rod system
for the air intake and exhaust
cam followers contribute to the
engine's easy and simple
maintenance. |
|
Over the past 8
decades Niigata has delivered a
total of over 20 million kWm of
diesel engines worldwide. The
22HLX is another beakthrough:
compact, high performance, high
output and environment friendly,
promising healthier returns on
the customer's investment. |
|
|
|
|
OPTIMIZED
COMBUSTION EFFICIENCY |
|
* NCCS (Niigata
Compact Constant Pressure Turbocharging
System).
* High maximum combustion pressure (Pmax)
of up to 20 MPa.
* Brake mean effective pressure of 2.44
MPa, mean piston speed of 10.0m/s.
* Output rate of 24.4 MPa.m/s.
* 147.1 MPa high pressure, short
duration fuel injection system.
* Cylinder liners equipped with fire
rings.
* Capable of burning low grade bunker
fuel of up to 700 cSt at 50 degC |
|
SPECIALLY
DESIGNED FOR HIGH RELIABILITY AND LOW
VIBRATION |
|
* Designed by FEM
(Finite Element Method) stress
calculation.
* Stress measurement confirmation by
component element tests.
* NCI (Nodular Cast Iron) highly
rigid monoblock double-walled hanger
type crank case.
* Special chrome-molybdenum steel forged
induction hardened crankshaft with large
main and
crankpin journals; carefully
counterweighted for high degree of
balance.
Very low vibration levels. |
|
SIMPLIFIED
MAINTENANCE AND INSPECTION |
|
* Four stud cylinder
head fastening.
* Wide air trunk and cooling water and
lube oil pipes built-in with crankcase.
* Special hydraulic tools for
disassembly and assembly work.
* Swing arm type cam followers.
* Unitized per cylinder segmented cam
shaft.
* Total weight reduced by 12%, component
parts reduced by 25%. |
MODEL |
6L22HLX |
8L22HLX |
12V22HLX |
16V22HLX |
18V22HLX |
Type |
Turbo charged, 4 cycle diesel engine
with air cooler |
Configuration |
In-line-form |
Vee-form |
Cylinders |
6 |
8 |
12 |
16 |
18 |
Bore |
220 mm |
Stroke |
300 mm |
Displancement |
11.40 L/cyl. |
Rotation direction |
Clockwise (Viewing from the coupling
side) |
Starting system |
By compressed air |
Fuel injection system |
Direct injection |
Cooling method |
Water cooled |
Turning method |
Hand drive |
Fuel oil |
Diesel oil or Heavy fuel oil |
MODEL |
6L22HLX |
8L22HLX |
12V22HLX |
16V22HLX |
18V22HLX |
Frequency |
50/60 Hz |
Max .
combustion pressure |
20 MPa (204 kgf/cm2) |
Mean
effective pressure |
2.44 MPa (24.91 kgf/cm2) |
Engine output for 50
Hz |
1 392 kWm |
1 856 kWm |
2 784 kWm |
3 712 kWm |
4 176 kWm |
(232 kWm/cyl.) |
Generator output |
1 320 kWe |
1 760 kWe |
2 640 kWe |
3 530 kWe |
3 970 kWe |
Engine
speed |
1 000 min-1 (1
000 rpm) |
Mean
piston speed |
10.0 m/sec |
Engine output for 60
Hz |
1 253 kWm |
1 670 kWm |
2 506 kWm |
3 341 kWm |
3 758 kWm |
(209 kWm/cyl.) |
Generator output |
1 180 kWe |
1 580 kWe |
2 380 kWe |
3 170 kWe |
3 570 kWe |
Engine
speed |
900 min-1 (900
rpm) |
Mean
piston speed |
9.0 m/sec |
>>
|
The output
figures shown in the tables represent
the rating under the following standard
reference conditions. If site conditions
are different from the standard
reference conditions, the output shall
be adjusted from the above figures.
Standard Reference Conditions : |
|
|
1) Ambient temperature:
40 degC
2) Cooling water (air cooler inlet)
temperature: 35 degC
3) Atmospheric pressure: 101.3 kPa (760
mm Hg)
4) Generator output is subject to
generator efficiency |
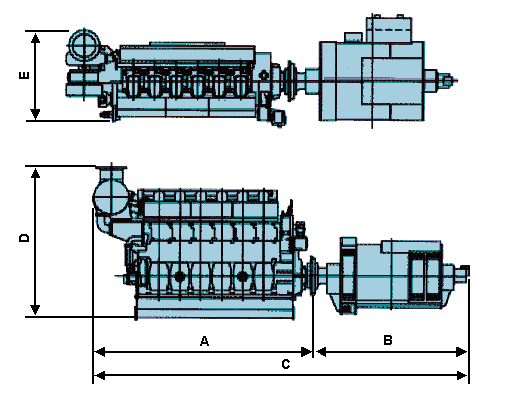
MODEL |
Principal Dimensions (mm) |
Mass (t) |
A |
B |
C |
D |
E |
Engine |
Generator |
6L22HLX |
3 390 |
2 730 |
6 120 |
2 730 |
1 693 |
12 |
6.5 |
8L22HLX |
4 130 |
3 100 |
7 230 |
2 847 |
1 693 |
15 |
11.0 |
12V22HLX |
3 680 |
3 250 |
6 930 |
3 192 |
2 080 |
20 |
12.5 |
16V22HLX |
4 480 |
3 490 |
7 970 |
3 192 |
2 080 |
24 |
15.0 |
18V22HLX |
4 880 |
3 590 |
8 470 |
3 192 |
2 080 |
27 |
16.5 |
Note: The mass and dimensions of generators
shall be subject to electrical design.
1 Crank Case |
A monoblock
hanger type structure made of
NCI (Nodular Cast Iron) for
sufficient strength and
rigidity, with low vibration
characteristics necessary for
the high Pmax of the engine. In
a simplified design, the crank
case incorporates the wide
intake air duct, the cooling
water main pipe, and lubricating
oil main pipe. |
|
|
|
|
2 Crankshaft & Main Bearings |
|
Forged from
special chrome-molybdenum steel
stock, the crank shaft is
capable of sufficient strength
to withstand the high Pmax of
the engine, made effective by
the large diameter of the main
and crankpin journals with
induction hardening. Kelmet type
metal bearings resist increased
surface pressure, prolonging
service life. Carefully designed
counterweights ensure a high
degree of balance, maintaining
sufficient and consistent
bearing oil film thickness. |
|
3 Pistons |
From Niigata's
own foundry, the piston is a
simple, monoblock construction
of Nodular Cast Iron,
lightweight but efficient for
high Pmax capacity. Fitted in
each piston are three
compression rigs (with a special
barrel type top ring) and one
oil ring, which, when
functioning together with the
fire ring in the cylinder liner,
reduces lubricating oil
consmption. |
|
|
|
|
4 Connecting Rods |
|
Of special
forged steel, the connecting rod
consists of a horizontal-split
large end bearing housing to
match the large diameter
crankpin for improved
reliability and reduced bearing
load stress. |
|
5 Cylinder Liners |
Fabricated with
special wear resistant cast
iron, the cylinder liner is
equipped with a replaceable
fire ring at the top portion
combustion zone. The upper
section of the liner embodies a
thick wall construction, for
high Pmax operation. The lower
section of the liner is
air-cooled to effectively reduce
cold corrosion wear. |
|
|
|
|
6 Cam Shaft |
|
The cam shaft
is a monoblock structure
composed of the cam and a large
diameter shaft, considering the
high injection pressure needed
for increased combustion
efficiency. The cam shaft's
segment type construction (one
segment is one cylinder) assures
very easy, simplified
maintenance. Each segment is
bolted axially to that of the
next cylinder's through a common
journal part. |
|
|
7 Cylinder Heads |
Made of CV
(compacted vermicular) cast iron
for even stress distribution and
better thermal conductivity, the
cylinder heads are of carefully
designed rib arrangement for
uniform rigidity and low
deformation under load. Cooling
water from the liner ascends
into the cylinder heads via
circumferential cooling bores
for the thick walled combustion
zones before exting to the
headers. The 4-stud design is
further adopted for wider intake
and exhaust ports and simplified
maintenance. Two intake and two
exhaust valves are arranged in
tandem for each head, with both
intake and exhaust ports located
at one side opposite the
camshaft side, simplifying
maintenance work. |
|
|
|
|
8 Exhaust Valves |
|
Nimonic
(special high corrosion
resistance alloy) valves have
mechanical rotomat rotators to
equally distribute heat and
ensure uniform contact for long
reliable operation. |
|
9 Fuel Injection Pumps & Fuel
Injectors |
A high pressure
fuel injection pump (monoblock,
closed barrel type), a mini-mass
injector, and a short cycle
injection pipe that goes through
the cylinder head all contribute
to higher combustion efficiency
and better fuel economy. The
injection nozzle spray holes are
specially treated to increase
the discharge coefficient, thus
improving combustion and
prolonging nozzle tip service
life. |
|
|
|
|
|
|
|
|